![]() (Observe, na foto acima, a erosão provocada pela cavitação nas pás das turbinas)
|
CARACTERIZAÇÃO DO PROBLEMA
Turbinas hidráulicas de grande porte apresentam o fenômeno da erosão por cavitação, pois apesar de grandes avanços nas técnicas de modelamento numérico em mecânica dos fluídos, ainda não se consegue evitar definitivamente o problema. Nas turbinas mais antigas, que ainda estarão em operação por pelo menos meio século, este problema é mais intenso, sendo economicamente inviável e tecnicamente complexa a substituição das mesmas. Desse modo, o processo de erosão deve ser mantido sob controle, o que é efetuado por deposição de material utilizando processos de soldagem, onde são necessárias quantidades da ordem de 1000 kg de ligas especiais de aço inoxidável por turbina. A qualificação do procedimento de soldagem torna-se um ponto crítico do trabalho. Se isto não for conduzido com rigorosos critérios, a deposição de material pode até ser realizada com grande produtividade, através da utilização do processo MIG/MAG, mas a resistência à cavitação do material reposto pode estar muito abaixo das especificações. Um ponto crítico na qualidade do depósito é o aparecimento de porosidades que são pontos nucleantes ao início do arrancamento de material pelo fenômeno da cavitação. Testes de laboratório têm mostrado forte dependência entre a homogeneidade da superfície e a resistência à cavitação, e também que a resistência à cavitação é muito maior em depósitos efetuados automaticamente do que em depósitos feitos manualmente. Tanto o aparecimento de porosidades como as deficiências de homogeneidade têm sua maior dependência na forma com que o material do eletrodo se funde e se deposita na peça. OBJETIVOS / METAS O projeto envolve o desenvolvimento da tecnologia e de um sistema automatizado capaz de realizar a recuperação de superfícies erodidas por cavitação em rotores de turbinas hidráulicas de grande porte. Seu elemento central é um manipulador com junta telescópica, integrado ao processo de soldagem, capaz de operar no pequeno espaço confinado no canal entre pás adjacentes do rotor.
|
Para atingir estas metas, será necessário:
- (a) desenvolver e construir um manipulador especial com uma junta telescópica, quatro juntas articuladas e sua unidade de controle, capaz de posicionar e orientar a tocha de soldagem e um sistema de medição a laser em todo o volume de trabalho confinado entre duas pás adjacentes de rotores de turbinas hidráulicas de grande porte com incerteza de posicionamento não superior a 0,4 mm;
(b) integrar um sensor de medição a laser tipo folha de luz no braço do manipulador e medir as coordenadas da superfície analisada da pá, combinando dados do sensor com o posicionamento e orientação do braço do manipulador com incerteza não inferior a 0,5 mm. Este sensor também deverá monitorar em tempo real e realimentar o sistema de posicionamento, conforme a morfologia dos cordões de solda;
(c) otimizar os parâmetros do processo de soldagem MIG/MAG robotizado e adaptar as fontes microprocessadas e demais equipamentos de soldagem para uso nas condições de operação na turbina;
(d) desenvolver o processo de plasma alimentado e robotizado para otimizar as características e a qualidade superficial do passe de acabamento do processo de soldagem;
(e) desenvolver o sistema de controle cinemático e dinâmico do manipulador;
(f) desenvolver programa de computador para gerenciamento de todos os módulos do sistema (manipulador, sensor e fonte de soldagem microprocessada), capaz de coordenar as operações de medição da superfície, soldagem e acabamento;
(g) desenvolver e implementar o processo MIG/MAG robotizado de duplo arame para maximizar a produtividade e qualidade do processo de deposição de material;
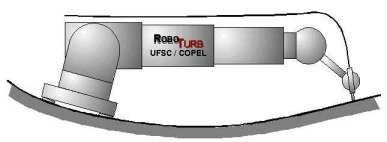
FINANCIADOR: MINISTÉRIO DA CIÊNCIA E TECNOLOGIA PADCT III
CO-FINANCIADOR: COPEL